More Comfort Equals More Safety. Find Out Why…
With Regards to PPE, More Comfort Equals More Safety.
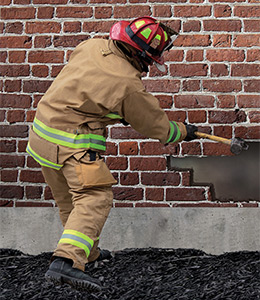
It’s true: PPE enhances safety ONLY when it’s worn the way it was designed to be worn. There are times when PPE isn’t worn
as it should because the user isn’t properly trained; other times it isn’t worn correctly because the user is trying to make
uncomfortable PPE more comfortable. Fire department PPE committees are tasked with thoroughly researching new technologies and conducting wear trials to ensure PPE items like turnout gear are not only protective and durable, but also comfortable.
Why Include Flexibility/Mobility/Comfort in the Risk Assessment and Specification of PPE Items Like Turnout Gear?
OSHA states the following in the Hazard Assessment document for selecting PPE (OSHA 3151-12Rf):
“Employers should take the fit and comfort of PPE into consideration when selecting appropriate items for their workplace.”
The reason for OSHA’s statement: PPE that is uncomfortable is significantly less likely to be worn in a manner that protects the
user from the various hazards the user will encounter. For example, if a bunker coat is stiff and uncomfortable, firefighters may
not zip up properly or clip all the hook and dee closures as specified in the department’s SOP; they may not flip their collars up
if the collar is too high (5 inches instead of 3 inches), etc. The following mindset follows: “nothing has happened yet, nothing will happen to me”. This dangerous behavior and the mentality that follows can be reduced or eliminated if the department specifies advanced designs and materials for better flexibility, mobility, and comfort…encouraging fire fighters to wear turnout gear properly.
Turnout Gear: Better Flexibility, Better Mobility, and Better Comfort are Possible.
Opportunities for improvements in the flexibility, mobility, and comfort of turnout gear can be achieved in a few ways:
1) Specify turnout gear garment designs that include ergonomic knees and elbows, better fit, better material utilization, etc.
2) Specify turnout gear materials (outer shells/thermal liners) with yarns and weaves that lead to better flexibility, mobility, and comfort.
Textile manufacturers aren’t responsible for the garment design but they certainly make all the difference in fabric design. By incorporating trusted and proven fibers like DuPont™ Kevlar® filament as well as unique weaving techniques such as Filament Twill Technology™, high performance fabrics for turnout gear become protective, durable, and finally—comfortable.
Fire Service Turnout Gear Fabrics: The Past and the Present
Fiber Options in Outer Shells and Thermal Liners:
The Past: 30 years ago textile manufacturers only made turnout gear fabrics with a few different fibers: DuPont™ Nomex® (USA), DuPont™ Kevlar® (USA), PBI (USA).
The Present: Today there are many more options: DuPont™ Nomex® (USA), DuPont™ Kevlar® (USA), PBI (USA); also several
foreign fibers: PBO (Japan), Technora® (Japan), Vectran® (Japan), Twaron® (Netherlands), Lenzing FR® (France). If you think the only thing in your fabrics today are fibers from DuPont and/or PBI (Made in the USA), ask the question and you may be
surprised with the answer.
Fabric Weight in Outer Shells:
The Past: 30 years ago textile manufacturers generally made turnout gear fabrics in heavier weights: 7.5 oz/yard2 was the standard.
The Present: Today there is a trend toward lighter weight fabrics:
7 oz/yard2 is becoming the standard and 6 oz/yard2 outer shells will be commonplace within five years.
Fabric Weave in Outer Shells and Thermal Liners:
The Past: 30 years ago textile manufactures made turnout gear fabrics with a plain or rip-stop weave. At the time, 100% spun yarns were the only yarn option available, leading to the need for a rip-stop weave for acceptable tear strength performance.
The Present: Today, plain weaves and rip-stops are becoming a thing of the past as twill weaves allow much more comfort and
flexibility. With the inclusion of filament yarns as is done with Filament Twill Technology™, twill weaves can be 2, 3, and even 4
times higher in tear strength than the strongest rip-stop weaves. A twill weave with spun and filament yarns adds more than enough strength plus recognized flexibility, mobility, and comfort…eliminating the need for rip-stop weaves.
Fire Service Turnout Gear Fabrics: The Future
The future of fire service fabrics is evolving: Firefighters want lighter and more flexible turnout gear without sacrificing durability
or protection. The next generation of break through fabrics will likely contain innovative fibers that are non-existent today:
think Star Wars. Until then, technologies like Filament Twill Technology™ in PBI Max™ and Armor™ outer shells and Glide™
thermal liners will continue to replace stiff and uncomfortable rip-stop weaves found in aging technologies.